Efficiency and quality improvement in CNC-production by incorporating additional and non-invasive sensors
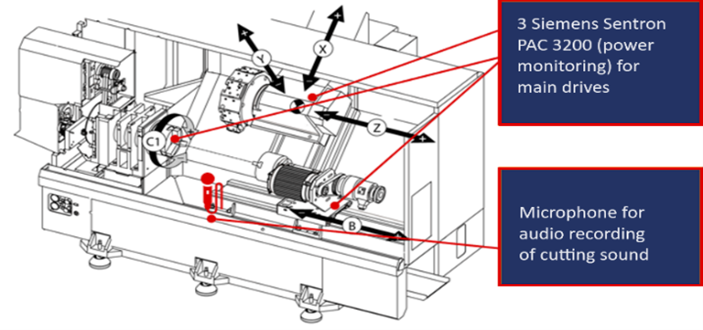
Failsafe Manufacturing Systems are designed to ensure a high level of reliability and quality in production processes. An important aspect of these systems is the integration of sensors and the combination of multi-sensor data, which enables early detection of potential failures. By detecting and addressing problems at an early stage, fail-safe manufacturing systems help to prevent quality issues and errors before they can occur, ensuring a more sustainable production process with less waste and greater efficiency.
A joint project involving the COMET centres Pro²Future and CDP and the universities TU Graz and WU Vienna will explore additional strategies to support failsafe manufacturing and predictive maintenance of production machinery. The use case for this project is the EMCO Maxxturn 45, a special model of a CNC (Computer Numerical Control) turning machine commonly used in manufacturing processes such as turning, milling, and drilling. These machines often do not have integrated diagnostic capabilities for failure detection, such as anomaly detection. Therefore, a prototype system was designed and developed, which is located in the Pilotfactory of the TU Vienna. The main part of the prototype is the aforementioned CNC Maxxturn 45 machine. The machine is equipped with external sensors that can detect vibrations in real time and react by adjusting the cutting parameters (see Figure).
Read full article: https://www.pro2future.at/wp-content/uploads/2024/05/2024-03-SuccessStory_CRPII_UC2_en.pdf
All Success Stories available via Research > COMET SUCCESS STORIES.