Ein innovatives modellbasiertes Konzept für eine effiziente und energiesparende Produktion von Kunststoffartikeln
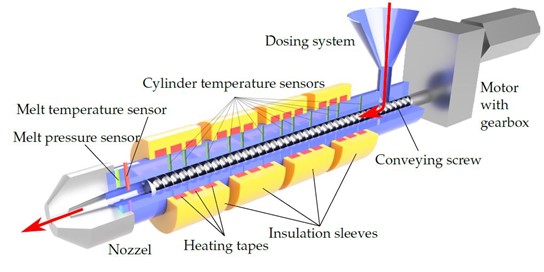
Ein wichtiges Verfahren zur Produktion von Kunststoffprodukten wie Verpackungen, Rohren etc., ist das Extrusionsverfahren. Dabei wird ein Kunststoffgranulat in eine Maschine, genannt Extruder, gefüllt, durch den Extruderzylinder mit einer komplexen Schnecke gefördert und dabei durch Druck und Wärme aufgeschmolzen. Die benötigte Wärme zum Schmelzen wird durch Reibung und Heizelemente, der Druck durch die Schnecke erzeugt. Druck, Massestrom und Temperatur der Schmelze sollen am Austritt vorgebbare Werte annehmen. Die neu entwickelte Regelung lässt den Extrusionsprozess schneller, effizienter und umweltschonender ablaufen, während gleichzeitig eine optimale Produktqualität sichergestellt wird.
Dieser Prozess soll möglichst energieeffizient und umweltschonend sein, aber auch verschiedenste Arten von Granulaten so extrudieren können, dass die Endprodukte hochwertig sind. So werden Extruderzylinder mit einer effizienten Isolierung ummantelt, wodurch ein Überheizen zu einer sehr langen Abkühlzeit führt, falls kein aktives Kühlen möglich ist. Die Herausforderungen sind daher heute Verzicht auf aktives Kühlen, sowie Verarbeitung von Granulaten mit schwankenden Eigenschaften, z.B. bei Recyclingmaterial. Standard ist, erfahrenes Personal stellt mittels Rezepturen den Extruder so ein, dass bei gleichbleibenden Bedingungen ein bestmögliches Verhalten erreicht wird. Zeitliche Änderungen durch Fehler oder Veränderungen der Zusammensetzungen der Granulate können nicht gezielt berücksichtigt werden. Auch müssen die Rezepturen aufwendig erstellt werden. Die moderne Extrusion stellt einen äußerst komplexen, zeitlich veränderlichen Prozess dar, wobei die bestmögliche Einstellung erlernt werden soll.
Alle Success Stories finden Sie unter Forschung > COMET SUCCESS STORIES.