An innovative model-based concept for efficient and energy-saving production of plastic articles
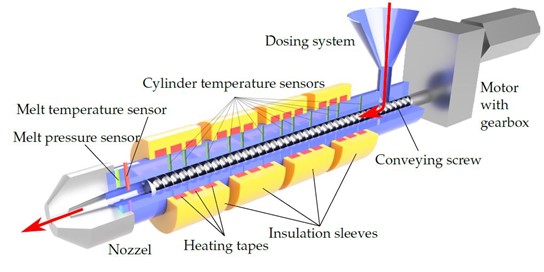
An important process for the production of plastic products such as packaging, pipes etc. is the extrusion process. In this process, a plastic granulate is filled into a machine called an extruder, conveyed through the extruder cylinder by a complex screw and melted using pressure and heat. The heat required for melting is generated by friction and heating elements, the pressure by the screw. The pressure, mass flow and temperature of the melt are to assume values that can be specified at the outlet. The newly developed control system allows the extrusion process to run faster, more efficiently and in a more environmentally friendly manner, while at the same time ensuring optimal product quality.
This process should be as energy-efficient and environmentally friendly as possible, but also be able to extrude a wide variety of types of granules in such a way that the end products are of high quality. Today’s challenges are doing without active cooling and processing of granules with fluctuating properties, eg. in recycling. The standard is that experienced staff use recipes to adjust the extruder in such a way that the best possible behavior is achieved under the same conditions. Changes over time due to defects or changes in the composition of the granules cannot be specifically taken into account. Recipes also have to be created in a complex manner. Modern extrusion is an extremely complex process that varies greatly over time, and the best possible settings have to be learned.
All Success Stories available via Research > COMET SUCCESS STORIES.